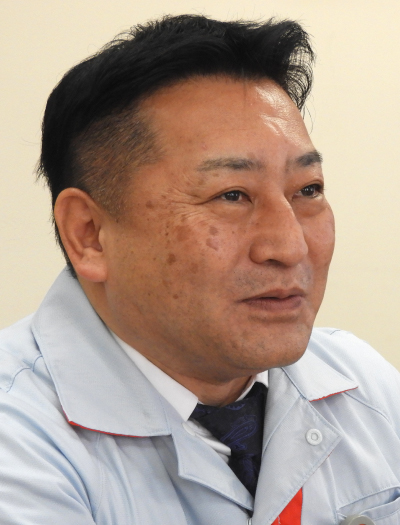
◆白井秀彰(シライ ヒデアキ)
㈱デンソー 先進プロセス研究部 機能創成研究2室 担当次長/工学博士(大阪大学)
【経歴】1969年生まれ。日本電装㈱(現 ㈱デンソー)入社後,生産技術開発部門に配属し,一貫して接合分野における技術開発業務を担当し,新しい加工プロセスの創出と技術開発を進めレーザー加工,抵抗溶接,アーク溶接など幅広い領域で多岐に亘り開発技術を立ち上げ自動車部品生産ラインでの実用化に成功している。現在は,先進プロセス研究部Project General Managerとして新しい領域での新技術創成プロジェクトに尽力している。受賞歴:溶接学会『田中亀久人賞』,軽金属溶接協会『論文賞』,レーザー学会産業賞『優秀賞』など多数受賞。レーザー加工学会理事,溶接学会商議委員幹事。
自動車業界が100年に一度の大変革の時代に突入していると言われて久しい。光・レーザー分野から見てもその潮流を感じ取ることができるだろう。なぜなら,EVや自動運転,ゼロカーボン実現など自動車業界のこうした動きに伴い,光・レーザーを求めるケースが増えてきているからだ。
今回のインタビューには自動車部品を手掛けるデンソーにおいて溶接プロセス技術を主導している白井秀彰氏に登場いただいた。白井氏はレーザー採用の比率は確実に高まっているとし,そのためのプロセス開発が重要な位置づけにあるとしている。
EV/PHV,自動運転へと進化する自動車分野にあって,その基幹部品の製造におけるレーザー加工プロセス技術が注目されているが,今何が求められているのか,そして何が必要なのかについて,白井氏に語っていただいた。
─今,自動車業界では何が起きていて,部品メーカーとしてはどのような対応が求められているのでしょうか
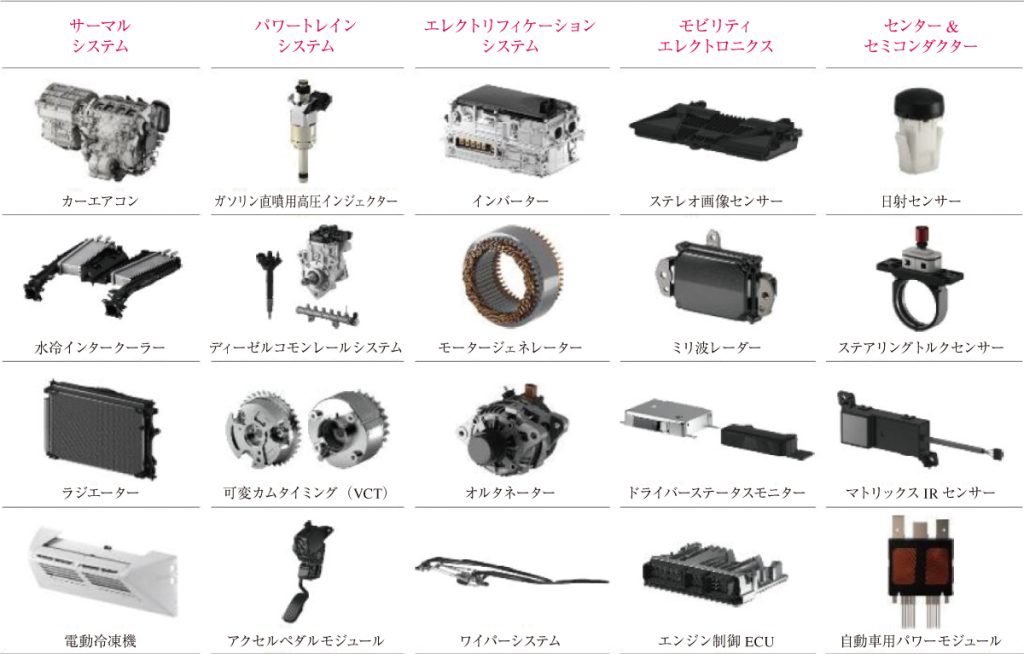
自動車の電動化という大きな流れがあります。そのために,これまで培ってきたコア技術だけでは勝負ができないようなところにまで来ています。自社では賄えない領域もあります。従って,グループ会社や関係会社も含めて色々なパートナーと連携するといった垣根を越えた対応が求められています。すなわち,『自前主義からの脱却』です。ともすれば,コンペティターとも協業・共創して取り組むといったこともあり得ます。
もう一つ大きな懸念は,中国メーカーとのコスト競争です。自動車部品を製造する側としては,やはり安くて良いものを安定的に供給するということが重要になってきます。この辺りが非常にデリケートで難しいところですね。
─競争相手というのは欧米よりも,むしろ中国の方が驚異的なのでしょうか
そうですね。マーケットのシェアを見ても,中国が台頭してきています。BYDも勢いがありますからね。一方で中国の内情を見ると,実に広いスペースにEVの新車が放置されている映像がニュースで取り上げられたりしていますので,よくわからない,よく見えないところもあります。ただし,技術開発のスピードは速いですし,即決即断力が必要となり日本企業にとっては厳しい時代になっているのは間違いありません。
また,カーボンニュートラル実現やSDGsを意識した取り組みも求められています。循環型社会を構築していく上ではマテリアルリサイクルし,それをリペア・リビルトしていくことも必要になってきています。こうした取り組みに並行して,サーキュラーエコノミー(循環経済)という観点でも物事を考えていかないと取り残されてしまう時代に入っています。
─自動車部品製造におけるレーザー加工の現状をお聞かせください
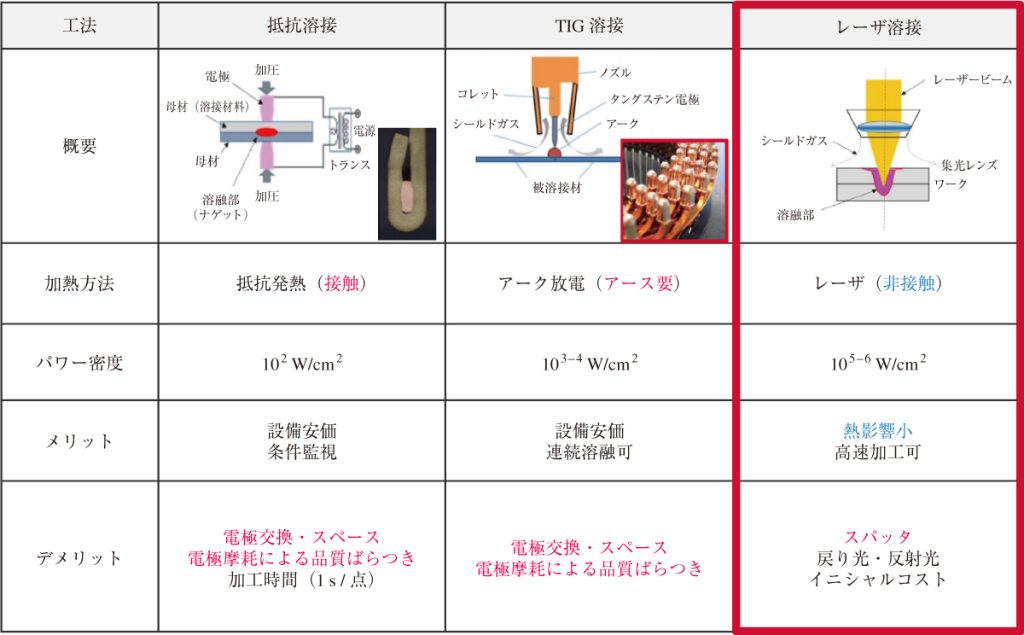
レーザーは,色々な部品の生産に使用されています。レーザーと一口に言いましても,波長や出力(パワー),照射時間によって実に多くのバリエーションがあるので,適材適所を見極めることが大事です。
自動車の電動化に伴うe-mobility部品の領域では,モーターやインバータにおいて銅材料が非常に多く使用されます。導電率が高いので非常に効率が良いため,幅広く使われていますが,如何にして銅材料の溶接を安定的に行なうかが重要になってきています。
これまで銅材料の溶接については,抵抗溶接やTIG溶接に加えて,レーザー溶接も適用してきました。抵抗溶接やTIG溶接は,エネルギーを発生させるために電極を用いるので,その電極の消耗が品質に影響してしまうという課題があります。レーザーは非接触で非常に有効ではありますが,銅材料に対しては,レーザーの吸収率が低い波長帯のレーザーが主流でした。従って,銅材料を溶接して強度や気密を確保するため,非常に大きなエネルギーを部材に投入する必要がありました。
しかしながら,スパッタの発生や熱影響の問題があり,従来の方法では,小さな構造部品では要求品質を満足し製品機能を成立することが難しい状況となり,大きな壁でした。我々は,従来のレーザーのデメリットをプロセス開発でメリットに生かせないかというモチベーションで技術開発に着手しました。