測量は,光学部品が要求される仕様に一貫して適合し,安全に機能することを確実にするうえで極めて重要になる。この信頼性は,ハイパワーレーザーを利用するシステム,もしくはスループットの変化がシステム性能に支障をもたらす場合にとりわけ重要になる。レーザーオプティクスの測定には,キャビティリングダウン分光法,原子間力顕微鏡法,微分干渉コントラスト顕微鏡法,光学干渉法,シャックハルトマン波面センサー,分光光度計を始め,広範な測量法が用いられている。
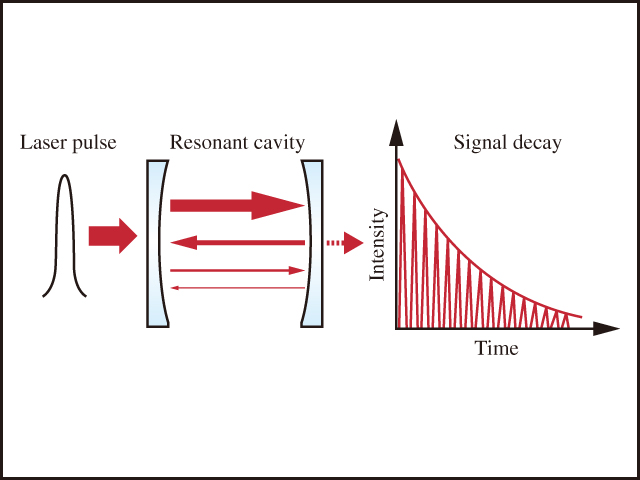
セクション1:キャビティリングダウン分光法
キャビティリングダウン分光法(Cavity Ring Down Spectroscopy;CRDS)は,気体サンプルの組成を判断するために用いられる測量法だが,レーザーオプティクスでは光学用コーティングによる損失を高感度に測定するのに用いられる。CRDSシステムでは,2枚の高反射ミラーで構成された共振器キャビティ内にレーザーパルスが送られる。
反射する度にごく少量の光が吸収・散乱・透過によって損失し,反射した光は共振器内を往復する。2番目のミラーの背後にある検出器が反射光の強度の減少(リングダウン)を計測し,この測定値がミラーの損失を計算するのに用いられる(図1)。レーザーミラーの損失の特性化は,レーザーシステムが所望するスループットを実現するかを確実にするためにも欠かせない。
キャビティ内部のレーザーパルスの強度(I)は次式で与えられる:
I0はレーザーパルスの初期強度,τは透過・吸収・散乱によるキャビティミラー損失の合計,tは時間,cは光速,そしてLはキャビティの長さになる。
CRDSで得られた値は,キャビティ全体の損失である。したがって,1枚だけのミラーの損失を決定するには,テストを複数回行なう必要がある。2枚の参照ミラーが最初の測定を行なうのに用いられ(A),次に2回の更なる測定が行なわれる:1回目は最初の参照ミラーを被験ミラーに置き換えた場合(B),2回目は他方の参照ミラーを被験ミラーに置き換えた場合(C)である。この3回の測定が被験ミラーの損失を決定づけるのに行なわれる。
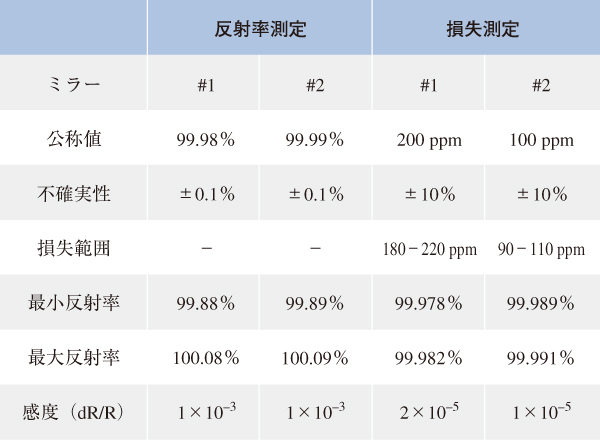
M1とM2は,2枚の参照ミラー各々の損失,M3は被検ミラーの損失である。ここでは,キャビティ内の空気中の損失は無視できると仮定する。CRDSは,小さな損失の量を正確に計測する方が大きな反射率を同様に計測するよりも遥かに容易であることから,反射型レーザーオプティクスの性能の特性化に最適な方法となる(表1)。
反射防止コーティングが施された透過型部品も,共振器キャビティ内に挿入して,それによる損失の増加量を計測することで試験できる。CRDSでは,ミラー上やキャビティ内部のいかなるコンタミも損失の測定に影響を及ぼすため,クリーンな環境で細心の注意を払って実施されなければならない。
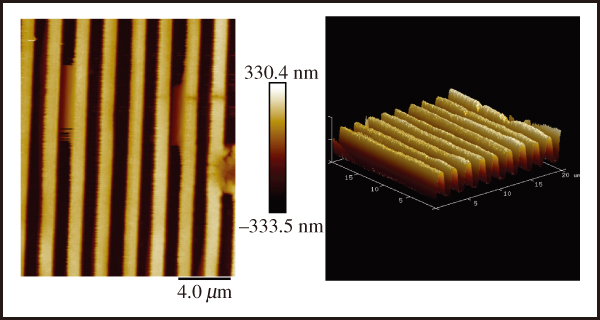
セクション2:原子間力顕微鏡法
原子間力顕微鏡法(Atomic Force Microscopy;AFM)は,表面トポグラフィーを原子分解能で行なう測量法である(図2)。極めて小さく先の尖った探針(チップ)でサンプル面全体をなぞり,面の3D構造を再現する。触針は,顕微鏡ヘッドの他の部分に繋がった矩形または三角形状のカンチレバーに装着される。カンチレバーの動きは圧電性セラミックによって制御され,これにより,カンチレバーの3Dポジションをナノメートル以下の分解能で確実に行なう。
レーザーオプティクスでは,AFMは光学部品の表面粗さを計算するのに主として用いられる。表面粗さは,レーザー光学系の性能に大きな影響を及ぼすことがある。なぜなら,それが散乱の主要な要因になることがよくあるからである。AFMは,面の3Dマップを数オングストロームの精度で作り出す。
触針は,試料に常時接触しながらその面をスキャンするコンタクトモードか,面と断続的に接触しながらスキャンしていくタッピングモードのどちらかになる。タッピングモードでは,カンチレバーはその共振周波数で振動し,その振動サイクル中の短い時間だけ触針が表面に接触する。コンタクトモードは,タッピングモードほど複雑ではなく,表面をより正確に再現する。しかしながら,スキャンニング中に表面を損傷させる可能性が高くなり,触針がより早く摩耗することから,触針の寿命はより短くなる。
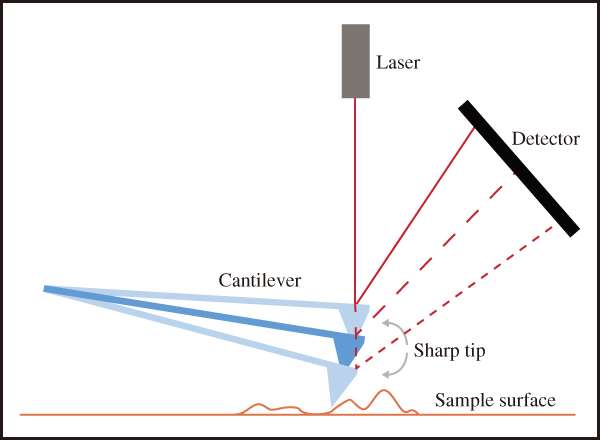
両方のモードとも,カンチレバー頭部で反射したレーザーがディテクター上に向かうことになる。試料面の高さの変化でカンチレバーが動き,それによって検出器上のレーザーの位置が変化することで,試料面の正確な高さマップが生成される(図3)。
触針の形状と組成は,AFMの空間分解能に重要な役割を担うため,スキャンを要する試料に応じて選択されなければならない。触針が小さくて尖っているほど,横方向の分解能はより高くなる。しかしながら,触針が小さければスキャンに要する時間が長くなり,大きなものよりも費用がかかる。
触針と試料面間の距離を制御することで,AFMシステムの垂直分解能が決まる。機械的及び電気的なノイズが垂直分解能を制限し,そのノイズレベルよりも小さな試料面の構造は解像することができない。触針と試料間の相対的な位置も,温度変化に起因するAFM構成部品の膨張や収縮に敏感になる。
AFMは時間のかかる測量法であり,試料面の100 µm×100 µm程度の小さな部分の測定が統計学的に製造工程全体を十分に再現できる場合の工程検証やモニタリングに主として用いられる。
■Metrology⑴
■Edmund Optics Japan Co., Ltd.
<お問合せ先>
エドモンド・オプティクス・ジャパン㈱
TEL: 03-3944-6210
E-mail: tech@edmundoptics.jp
URL: www.edmundoptics.jp