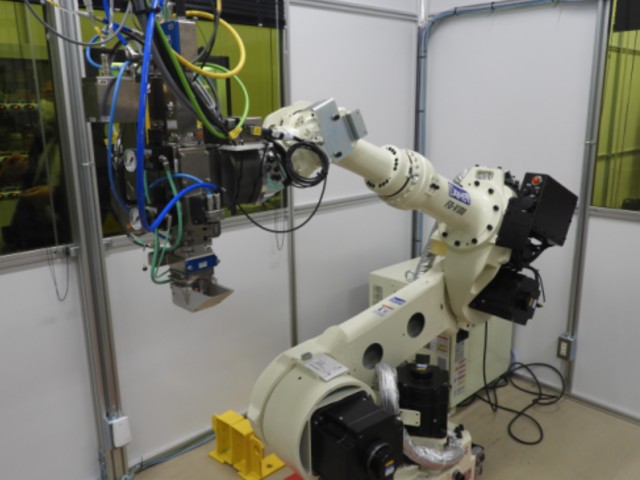
高出力ダイレクトダイオードレーザーを手掛けるレーザーラインは,加工ヘッド・光学測定メーカーのプレシテック・ジャパンと共同で,システムインテグレータの豊電子工業・豊明工場内に最先端レーザーリモート溶接によるテスト加工が可能なラボを開設した。同社にとっては品川ラボに続くもので,自動車産業が集積する中部地区への設置の必要性を判断した。
今回新設したラボには,レーザーリモート溶接システムと3D切断加工システムの2台が設置され,システムはレーザーラインの品川ラボでも使用されているダイヘン製のロボットを組み合わせたものになっている。
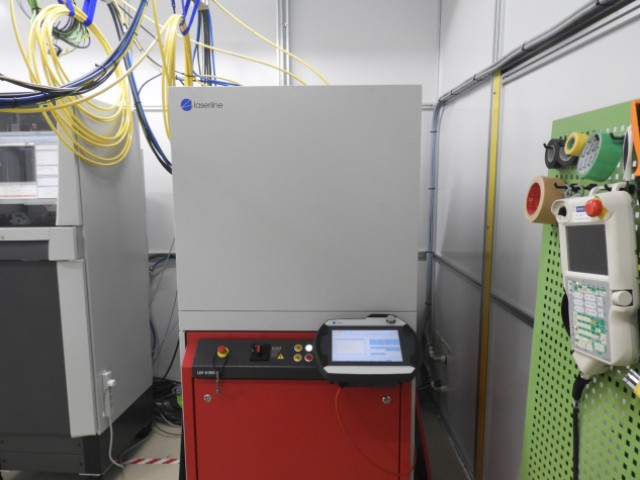
搭載しているレーザーは出力8kWのコンバーターレーザー「LDF8000-6」で,フィールドでも交換が可能な,高輝度を向上させるビームコンバーターモジュールをダイレクトレーザダイオードに取り付けることにより,コア径200μmと150μmのファイバーケーブルを2分岐したものとなっている。
加工ヘッドはプレシテックが担当し,溶接には1軸リモート溶接ヘッド「WeldMaster」が,切断には3D加工ヘッド「SolidCutter」が搭載されている。このうち,リモート溶接ヘッドは,シームの位置,高さやギャップ幅などの位置や形状を検出するプリプロセス,溶接中の金属溶融状態を検出し,プロセス条件へとフィードバックするインプロセス,溶接後のビード形状の測定といった品質検査を行なうポストプロセスの3つのモニタリングをリアルタイムに行なうことができる。
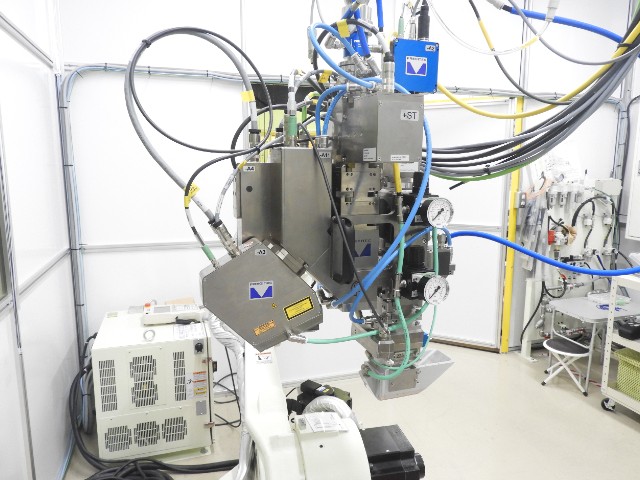
このシステムではレーザー出力制御によって溶け込みに関わる入熱量もコントロールできることから,フィラーワイヤーが不要な加工を実現する。この特長は特に融点が低く,熱伝導率が高いアルミ材に対して有効とされる。
今回のレーザー加工システムの設置にあたって豊電子工業はレーザー加工条件などシステム全体を制御する装置の開発を担当した。同社にはレーザーラインにとって国内販売1号機となる出力1kWの青色ダイレクトダイオードレーザーが導入されており,銅加工システム事業を展開している。
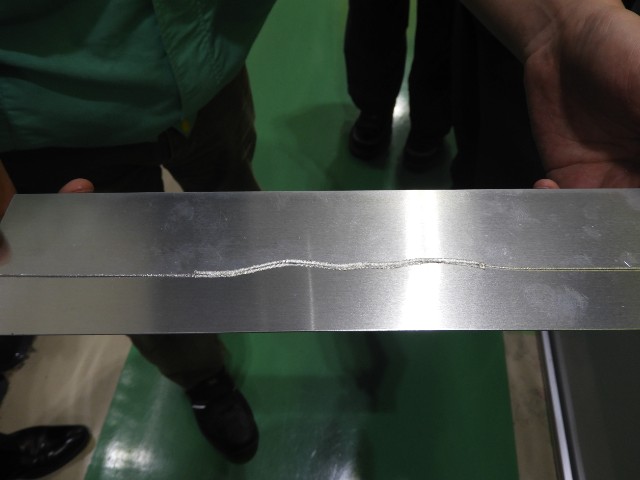
同社はシステムインテグレータとしてロボットを中心とする設計から開発,保守サービスまで生産ライン全体を一括して構築しているのが強みで,国内に4つの製造拠点、海外には6カ国の製造・販売拠点を持つ。同社ではレーザー加工事業にも注力しており,今回設置したレーザーリモート溶接技術のシステム提案も行なうとしている。
近年,自動車分野では燃費向上の観点から構成部材の軽量化に向けてアルミ合金の採用が進んでいる。今回の最先端レーザーリモート溶接システムは,既に欧州自動車メーカーの量産ラインに導入されており,その生産効果を高めているという。実際,アルミのレーザーリモート溶接ではサイクルタイムが53%改善され,さらにCO2排出量が24%,ラインニングコストが95%とそれぞれ削減につながったとしている。
加工においてもシビアな条件が求められる自動車分野にあって,実績あるこうした先進レーザーリモート溶接システムの日本市場での展開の今後が注目されるところだ。