1. はじめに
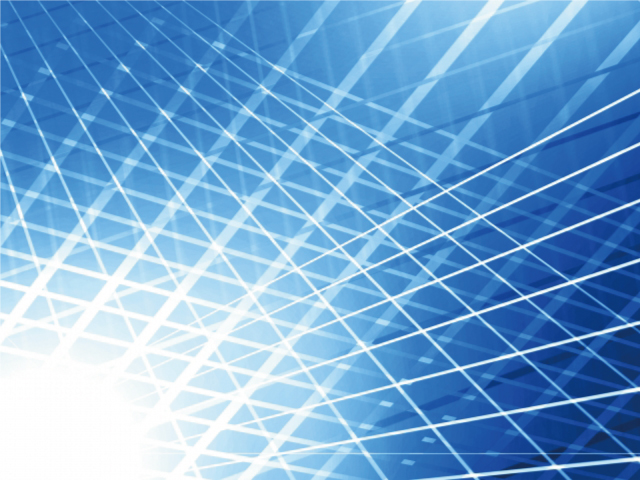
プリンテッドプロセスはインクベースの技術であるため,インク化が比較的容易な有機材料が多く用いられ,様々な有機半導体などの開発が現在も進んでいる。有機材料は使い捨て応用には良いが,安定性が求められるアプリケーションでは不都合な場合も多い。例えば,自動車を考えれば,夏場は高温多湿で強い紫外線にさらされ,冬場は氷点下といった車室内センサー形成への応用は必ずしも適してはいない。そのような中,我々は,機能性セラミックスを低出力レーザーでマイクロ“印刷”する手法を開発した。セラミックスは極めて高い物理的/化学的安定性を備え,導電性や絶縁性,発光性,生体親和性,磁性,圧電性などの幅広い機能性から,エレクトロニクスやフォトニクスなどで数多くの産業応用がなされてきた。一方で,その加工は難しく,配線化には高温焼成過程や複雑な工程が必要であり,インク化も容易ではなく印刷製造への展開は簡単ではない。
レーザー照射による機能性パターン形成プロセスは40年以上前から報告がある。集光スポットで生じる光重合や光還元,焼結,除去,格子欠陥生成,高密度化などを介して局所的に材料の加工が行われる2〜7)。定番の応用例はマイクロ導電配線の直接描画であり,AgやCuなどの配線描画は非常に多くの事例が積み上げられてきた。半導体プロセスの繰り返し工程を考えれば,レーザー描画は非常に簡便な手法であるが,現在に至るまで解決されていない大きな技術的課題が存在する。それは,被加工材料に適切な感光性が必要とされる点である。レーザー加工を含む光加工では,光を吸収しない,あるいは,吸収しても適切な光反応経路を有さない材料には適用が難しく,この感光性による材料制限は光加工における原理的課題とも言える。
その意味において,高い透過性を持つ酸化物ガラスなどはレーザーにとっては難加工材の一つである。一般的には,この問題を解決するため,被加工材料に新たに感光成分を添加するか,被加工材料が元々持っている吸収帯に合った発振波長を持つレーザー光の探索がなされることが多い。しかしながら,前者では不純物を添加することとなり,後者では光が吸収されたとしても所望の加工現象が進行するとは限らない。このような材料選択上の限界は,レーザー直接描画プロセスの適用範囲を大きく制限してきた。