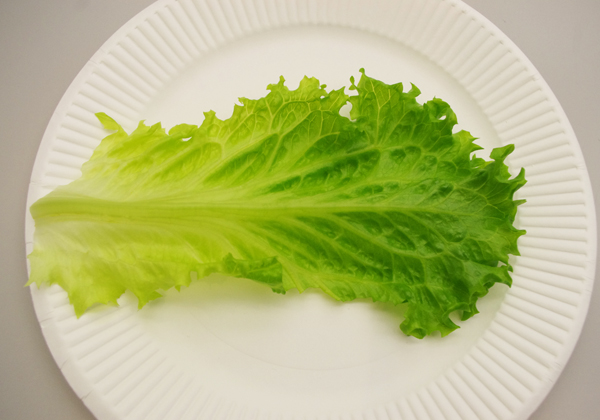
パナソニックは植物工場ビジネスに本格的に参入する。同事業では後発となる同社だが,これまでの植物工場の問題点を洗い直した「工業的アプローチ」による再現性の高い野菜成育技術の提供により,現在8割が赤字とも言われる植物工場を,持続可能なビジネスとしてバックアップする。
同社はこれまでの植物工場の一般的な課題として,①不均質な栽培環境②高い運営コスト③メーカ課題 の3つを指摘している。今回,これらに対する同社の対策と取り組みは以下のようになっている。
不均質な栽培環境
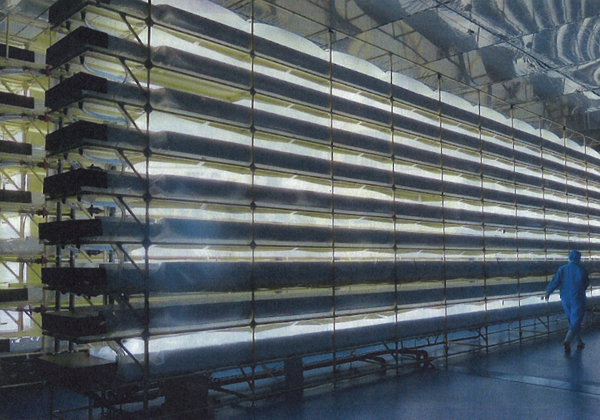
多段にした生育棚では上段と下段で温度差ができるが,国内最大級の工場ではその差は約10℃に達し「季節が異なる」ほどになる。このため野菜の育成スピードに差が出るほか,重量歩留まり(規定重量まで生育する割合)は60〜70%程度だという。
この課題に対して同社は今回,「特殊空調技術」を新たに開発した。詳細は公開していないが,育成棚の位置や高さによらず温度を均一に保つ技術で,棚間の温度差を1.5℃以内に保つことが可能となる。これにより重量歩留り95%を達成できるとしている。残りの5%については種子の問題であり,これ以外はほぼ理想的な育成ができるという。
高い運営コスト
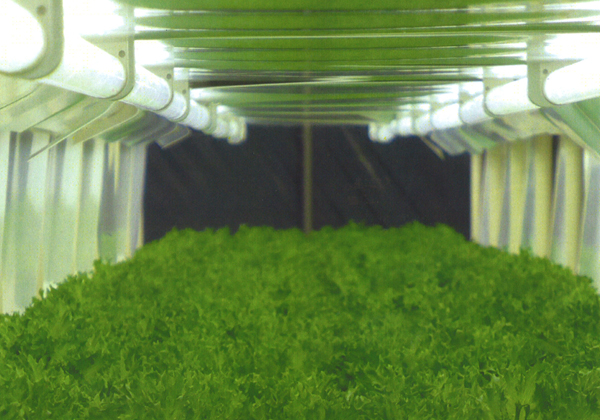
植物工場の運営コストは,電気代と人件費が大きなウェイトを占める。照明とそこから出る熱を下げる空調に占める割合が大きく,運営費の30%程度となっている。また自動化への取り組みが不足していることから,人件費も大きな問題だと同社は指摘する。
これについて,先の「特殊空調技術」が電気代の削減に一役買う。植物工場ではLED光を効率的に利用するため,反射板を棚を囲うように吊り下げるが,熱がこもる原因にもなるため一定の隙間が必要だった。今回の空調技術により,反射板を隙間なく設置することが可能になったため,LEDの数を半分に減らしながら,同等の照度を確保した。
さらに同社がメーカとして工場で長く培ってきた省エネのノウハウを導入することで,電気代と蛍光灯を用いた他メーカの植物工場と比して50%以上,LEDを用いた植物工場との比較でも30%以上削減することができたという。
また,育成プレートの移動や包装・検査に自動化技術を導入することで,日産2,000株の植物工場で必要だった従業員数を8名から6名に減らすことが可能だとしている。将来的には仮植や定植も自動化するなど,さらなるオートメーション化を目指す。
メーカ課題
ここでのメーカ課題とは,植物工場業界全体の課題でもある。明確な基準が無かったため,メーカが生産能力を提示するときに使う「株」の定義が曖昧だったことや,波長ごとにパラメータの設定が可能なLEDランプの特性を活かした栽培ノウハウを持っていないこと,さらには工場施工の経験の無い業者が多いことも指摘している。
これに対して同社は先の「重量歩留り」という概念を導入し,生産能力を明確化すると共に,サイズや味,見栄えについても規格化して均質な野菜栽培の指標とした。
こうした指標を達成した野菜作りのために同社は,LED栽培ならではの「栽培レシピ」を開発している。同社は赤色LED(660nm),と青色LED(波長非公表 450~500nm)を光源に用いている(上の写真は撮影用に蛍光灯/白色LEDを使用)が,パラメータを操作することで味や食感を制御するほか,低カリウムなどの機能性野菜などのレシピも提供できるとしている。
同社はこうしたレシピ開発を福島県工場での実証栽培を通じて行なってきた。その中で栄養素地を保証できる機能性野菜の開発などで順調な成果を上げており,生産したレタスを県内30店舗のスーパーに卸し,一般的な露地物のレタスと同程度の価格(198円前後)で販売している。
他社にはない付加価値
このように植物工場を徹底的に工業化するとで,同社は農業がターンキービジネスになるとみている。建屋さえあれば,同社がメーカとして培ってきた工場の施工から運営までのノウハウを提供する。
さらにITCを活用し,育成状況を常時監視するだけでなく,トラブル時にはウェアラブルカメラを用いた遠隔サポートも用意しており,栽培ノウハウを持たない異業種であっても「マウスクリック栽培」による野菜工場事業への参入が可能だとしている。
同社ではこの植物工場の価格について,生産能力2,000株/日 規模の工場(床面積1,000㎡以上)で2億円,そこから1,000株増えることに+1憶円が目安になるとしている。この価格は他社の同規模の植物工場とほぼ同じだという。また,ビジネスモデルとして減価償却7年(消耗品費を含む)を提示する。
なぜ今参入?
植物工場が大きな話題となり,各企業がこぞって参入を発表したのは2~3年前のことだ。それに比べると今回のパナソニックの決断は随分遅かったようにも思えるが,その理由については光源のコストと性能の問題があったようだ。
パナソニックは植物工場を事業化するだけの技術とノウハウを持っているとかつてより言われていながらも,「3年前だったら参入していない」(開発担当者)と言うように,LEDの性能の向上と低価格化が今回の決断のポイントとなった。かつてはイニシャルコストの問題で蛍光灯を使う植物工場も多かったが,植物工場においてLEDの優位が揺らぎないものになったということだろう。*
*同社植物工場は蛍光灯もラインナップしている。
課題
今回,同社は厳格な品質管理を通じて農業を工業化し,野菜を「工業製品化」することで植物工場に新たな付加価値を見出すと共に,収益においても黒字化を眼に見える形で示すことで,後発ながらも大きなプレゼンスを見せようとしている。
しかし,同社は野菜の販売ルートを持たないことから,出口戦略まで顧客に提供するには至っていない。これについては流通業界とも折衝しているようだが,この出口までを絵に描いてこそ「マウスクリック栽培」に興味を示す顧客が増えるのは間違いない。
今後はスーパーなどを狙ったB to C戦略だけではなく,植物工場の強みである無農薬・低菌環境や,年間を通じた安定供給,さらに同社が強みとする味や食味のコントロール,規格化などを武器に,洗浄コストが6割を占め,異物混入などのトラブルにも悩まされているカット野菜業者などをターゲットに,B to Bへの需要も開拓していきたいとしている。