3Dプリンターの活用が盛んな米国,欧州では,かつてブームの頃に語られた誰もが何でも作れる革命的な道具から,ノウハウとスキルを持つ製造のプロが使う付加製造(AM:Additive Manufacturing)として進化を続けてきた。近年,M&Aによる買収や需要変化による業績悪化に翻弄されるようなAM企業もあるが,これらもさらなる進化のための新陳代謝と言えるだろう。
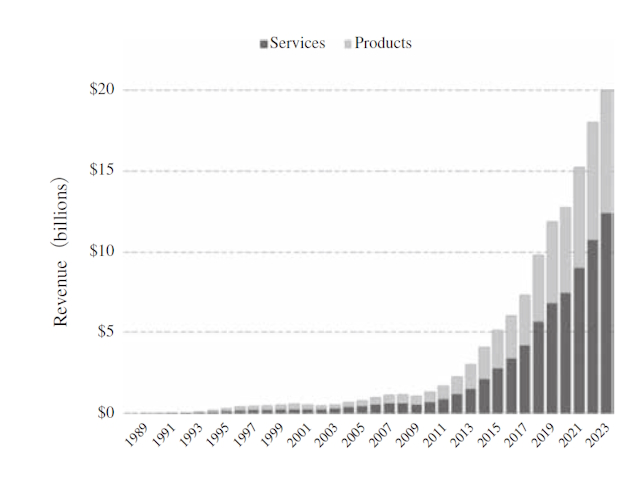
日本3Dプリンティング産業技術協会では,米国,欧州での最大規模の3Dプリンター展示会である,rapid+TCTおよびformnext を毎年現地調査し,市場,造形技術等の動向調査を行っている。また,米国,欧州の研究機関や大学を訪問し,最新技術の調査も行っている。これらの調査をもとに,AM/3Dプリンターにおける課題と動向を整理し,今後の展開を予測していく。
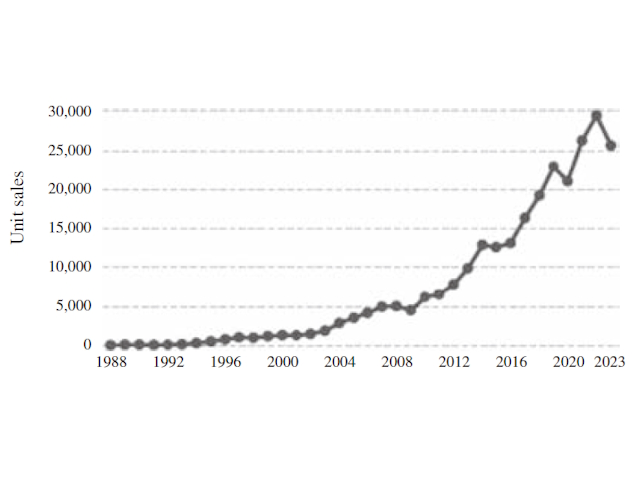
1.市場動向
3Dプリンターの世界全体の市場規模は,図1に示すとおり製品とサービスを合わせて2023年時点で約200億ドルである。2020 年はコロナ禍の影響で成長が鈍化したものの,2010年代は約20%前後,2020年以降は約10%代の成長率を維持しつつ順調に成長している。2010年代中頃からサービスのほうがシステム(装置)の売上を上回っており,世界全体では健全に市場が成長していく様子が伺える。
一方,日本の状況であるが,製品とサービスを含めた統計データを探してみたが,筆者が知る限り公表されていない。そこで,市場成長の中核を担う産業向け装置の台数規模を見ると,図2に示すとおり全世界で約25,000台の装置が出荷されている。少々の変動は見られるが概ね成長軌跡を辿っていると言えるだろう。図3の国内業務用装置の台数と比較すると,日本の占める割合は世界全体の10%程度であることがわかり,世界の中でも導入される装置数の比率は小さくないことがわかる。
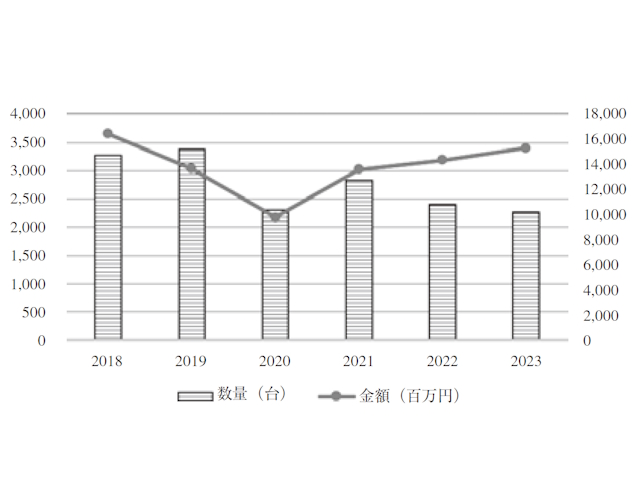
よく言われることとして,日本のAM市場は世界に比べて現時点では非常に小さいということが挙げられる。統計データがないので検証できないが,世界のAM市場規模は時間をかけて成長を続けており,その中で日本のAM市場も,前述の国内装置数データからインフラは整っていると言えるので,今後の成長が期待できるのではないだろうか。
2.造形技術の動向
本章では,主流の材料である金属と樹脂に近年広がりを見せているセラミックスを加えて,材料別に造形技術の動向を述べていく。表1に代表的な方式・材料についてまとめたので,適宜参照されたい。

2.1金属造形技術の動向
これまで,航空宇宙・医療・自動車レースなどの高コストであっても絶対的な高性能を追求する高付加価値分野で金属造形は発展してきた。これら高付加価値分野では,さらに価値を高めるため,ロケット部品など大型化の傾向が見られる。また,今後の普及が見込める自動車分野や消費者製品など最終製品の量産に向けての活用が期待されている。そのため,量産分野では高速化,品質安定といった量産上の課題を解決する技術の開発が進んでいる。

1)大型化
大型化の動向であるが,DED方式の利用が広がっている。3Dプリンターの造形原理は,付加製造という名のとおり,材料を少しずつ付加していくことにより自由な形状や構造の製造していく。多くの方式では付加する単位として水平面上の薄い層で行っているため,水平面上でしか造形できないという制約がある。
DED方式では自由な角度から造形できるので,多軸ロボットアームと組み合わせて図4に示すスクリューなどの自由曲面形状の大型部品を製造できる。また,造形速度も高速であるため,大型部品との相性もよい。アムステルダムではMX3D社のプリンターが橋の建築に用いられた実績がある。PBF方式の大型化には2つの種類がありPBF方式で用いられる粉末床の垂直拡張と水平拡張である。粉末床とは,材料の粉末を収めておく箱であり,造形物の最大サイズは,垂直方向および水平方向ともにこの中に収める必要がある。

垂直拡張は粉末床の水平方向のサイズはそのままに粉末床を垂直方向に拡張したものである。ロケット部品など縦長の部品の製造に適しており,金属の装置のレーザーユニットや筐体に大きな変更を加えずに部品を大型化できるメリットがある。AMCM社はEOS社の製品をベースに拡張をすることにより,図5に示す1 m以上の高さのあるロケット部品の製造を可能にしている。水平拡張は粉末床を水平方向に拡張したものである。こちらは,レーザー本数を増やしてマルチレーザーとして水平方向のスキャン範囲の拡張が必要であり,それに伴いレーザーの制御プログラム等に改変を加える必要がある。BLT社は図5に示す1 m以上の幅がある自動車のリヤサブフレームの製造を可能にしている。

2)高速化
高速化の動向については,BJT方式の実用化,新データ形式による転送速度向上,自動化などによる各種作業時間の削減などが挙げられる。BJT方式では,金属粉末層の上からインクジェットによりバインダーを噴射することでグリーン体と呼ばれる形状を造形する。グリーン体を取出した後に脱脂・焼結することにより効率よく金属造形物を得ることができる。この方式の装置は数社から発売されているが,脱脂・焼結プロセスでの形状収縮という課題がある。しかし,近年,実用的な部品が造形できるレベルまで進んできたようだ。GE社のAM部門であるColibrium Additive社は,図6に示す複雑な部品を展示会で展示していた。

新データ形式による転送速度向上については,従来のデータ形式は,STL形式に代表される三角形近による方法が主流であった。三角形のデータは平面と3 頂点の座標値で表されており,複雑なデータを処理する必要がないので,CPUやネットワークにかかる負担は少ないのがメリットであった。しかし,近年,造形形状の複雑化や大型化が進み,STL形式のデータ量の増大を招いている。また,AMではラティス構造という軽量化と強度を両立させる細密な内部構造をよく用いるが,三角形近似で表すと非常に多くのデータ量が必要になる。その結果,システム間のデータ転送に数時間を要するなどの問題を引き起こしている。

nTop社のインプリシットモデリング形式は,関数ベースのデータ形式であり,複雑なラティス構造であってもコンパクトなデータ量になるため,データ転送に時間がかからない。また,GPUとの相性もよく表示やデータ処理にも時間がかからないというメリットを持っている。このnTop社のインプリシットモデリング形式データを他社でも採用する動きが始まっており,システム間のデータ転送速度向上が促進されていくと思われる。

図7は,nTop社のモジュールを組み込んだMaterialise社の造形ソフトを使って,Nikon SLM Solution 社のPBF装置で造形を行ったものである。自動化などによる各種作業の削減であるが,各工程で工夫がなされている。ここでは設計および後処理の工程の事例を示しておく。設計工程では,従来はシミュレーションや実験により造形物の形状設計・構造設計を行っており,非常に長い時間を要していた。

また,生産準備として,性能や生産性を上げるために部品の配置や方向などの検討にも時間がかかっていた。近年は,用途に応じた自動設計・自動配置を行う設計ソフトが普及している。極端な例としては,すでに設計済のパターンから選ぶというところまで進化している。また,既存システムのどの部分をAM部品とすれば良いのかCADを読み込んで解析し推奨するソフトまで登場している。
後処理工程に関しては,金属造形では,デパウダ(粉末除去),サポート除去,造形物の表面処理(磨き)が必要となる。これらの後処理の自動化が進んでいる。デパウダに関しては設計データを読み込んで解析し,部品を回転させながら粉末を自動的に除去する装置がSolukon社から販売されている(図8)。

また,サポート除去に関しては自動化装置の開発も進んでいるが,サポートレス設計プロセスが各社から提供されている。設計段階からサポートをできるだけ減らせるようにコントロールするもので,サポートが少なければ,その除去の時間を大いに削減できる。

造詣物の表面処理に関しては,PBF方式での造形物は,表面はザラザラしており,耐久性,特に疲労破壊強度への影響が懸念される。そのため,品質安定化の観点で,実部品では表面を平滑にする後処理が求められる。ブラストなどの物理的な方法もあるが,自動化の観点で,電解研磨(乾式,湿式)などの化学的方法などが提案,実用化されている。
2.2樹脂造形技術の動向
樹脂造形においては,金属と同様に大型造形物の需要がある。また,樹脂造形はすでに量産が金属造詣よりも進んでおり,コスト低減や生産性向上の取り組みが進んでいる。
1)大型化
大型化に関しては,車のバンパーなどの大型部品の型枠,ディスプレイ,建築用型枠などの需要があり,メータサイズの巨大な造形が可能である。大型のMEX方式の造形装置では,射出成形等で使われるペレットをそのまま使えるスクリュー内蔵型のペレットエクストルーダーが普及しており,大型のガントリー形式の装置や多軸ロボットアームと組わせて利用する。材料自体がフィラメントと比べてコスト面で有利であることや異種材料のペレットを混合して利用できるというメリットもある。
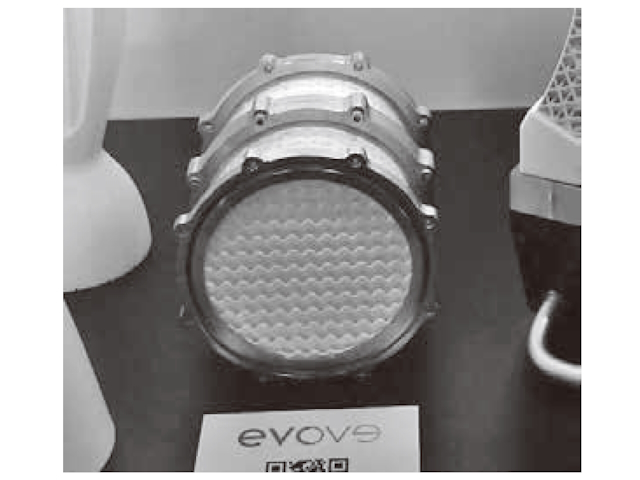
図13 Evove 社設計のフィルター部品
CEAD社はペレットなどの材料供給装置も含めた大型エクストルーダーを開発して販売している。熱を加えないタイプのエクストルーダーも販売しており,建築用のエクストルーダーとしても高いシェアを誇っている。WASP社の装置はカラフルなカラーグラデーションが可能である。LFAM(Large Formant Additive Manufacturing)と呼ばれる大型の多軸ロボットアームのシステムプラットフォームをAi Build社が提供しており,多くのパートナーが利用している。
2)コスト低減
PBF方式の装置はもともと生産性が高く量産向きであるが,さらにコスト低減を追求する動きがある。PBF方式のコストは造形領域の高さに比例するため,何個の部品を効率的に配置して造形するかで部品1 個あたりのコストが変わってくる。図10に示すようにHP 社の3DBuild Optimizerでは部品の配置密度を向上させることで,従来より30%のコスト低減を達成している。EOS社のP3 NEXT装置では,材料リサイクル率を80%に向上させることでさらなるコスト低減を引き出している。
3)生産性向上
VPP方式の装置では,従来は主に試作で使われていたが,生産性を向上させることにより最終製品への適用が進んでいる。具体的にはUV硬化樹脂にレーザーをあてることにより造形を行っていたが,レーザーからプロジェクタやLCDに変更することで,点から面に飛躍的な生産性の向上を果たした。さらに図11の大型ビルドプラットフォームや,図12の高速露光ヘッドにより生産性を向上させている。また,UV硬化樹脂による造形物で必要な洗浄などの後処理等ワークフローを自動化することによりトータルの生産性向上を達成している。
2.3セラミックス造形技術の動向
セラミックス材料は耐熱性,低熱膨張率,生体適合性などの特徴があるが,従来工法では複雑な形状を作成することが困難であった。UV樹脂に材料を分散させたものをVPP方式で造形した後焼結することで3D造形物を得る装置が数社から発売されている。また,造形エリアが従来の2 倍となる装置が発表されている。これにより,部品の大型化や量産化が加速すると思われる。Lithoz社の装置は造形エリアの体積が従来の約5倍にまで拡大されている。実際に活用されている事例もあり,Lithoz社の造形装置によるEvove 社設計のフィルター(図13)やStainbagh社の手術用ロボットのチューブなどが顧客事例として公開されている。
3課題と今後の展開
冒頭に述べたように,3Dプリンターは欧米では付加製造法として定着しており,米国をはじめとして3Dプリンター利用を推進し,製品製造へ応用していくという機運が高まっている。その背景には,設計の自由度の高さ,それによる付加価値の発現,部品の軽量化,部品点数削減といった3Dプリンターのメリットの理解が進んでいることがあげられる。
今後の展開としては,大型化,自動化,コストダウン,品質安定性の向上,標準の整備といった量産化に向けた開発がより一層進んでいくと予測する。その背景には,基本的なAM造形方式はほぼ固まってきているが,それぞれ一長一短があり,各社の技術開発も継続しており,進歩の余地はまだあると考えられるからである。実際,最も古い3Dプリンターの方式であるVPP方式ですら,本記事で解説したように,ここ数年,画期的な進歩を遂げている。また,装置面だけでなく材料面からのアプローチにより,短所を改善していくことで,さらに活用範囲が広がっていくものと期待する。
参考文献
1) Wohlers Associates, Wohlers Report 2024, https://wohlersassociates.com/product/wr2024/
2) ㈱中日社,2024 年版3Dプリンター/ 造形機の国内市場,https://www.chunichisha.co.jp/3d-printer.html
3) 日本規格協会,日本工業規格 JIS B 9441:2020,https://webdesk.jsa.or.jp/books/W11M0090/index/?bunsyo_id=JIS+B+9441%3A2020
本号の購入はこちら
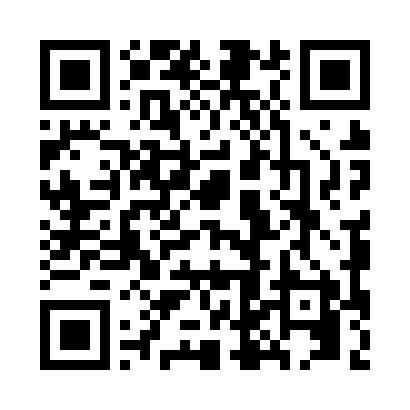