炭素の原子シートであるグラフェンは,シリコンの100倍以上のキャリア移動度を有し,高い光の透過率(97.7%),フレキシブルで高い機械的強度(ヤング率 1TPa)など,これまでに無いユニークな物性を持ち,大面積シートが実現できればタッチパネルの透明導電膜など光学材料にも応用できるとして注目を集めている。
現在研究が進められているグラフェンシートの主な作製方法には,①酸化グラフェンの剥離②SiCの熱分解③気体炭素源を用いたCVD法,の3つがある。しかし現在のところ,いずれも産業に供するのに十分な大きさや特性を備えたシートの量産には至っていない。
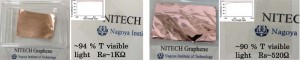
今回,名古屋工業大学大学院 未来材料創成工学専攻 種村研究室助教のカリタ・ゴラップ氏らの研究グループは,上記③のCVD法について,気体炭素源の代わりに固体炭素源を用いてグラフェンを作製する方法を考案した。これまでのCVD法はメタン(CH4)などのガスを炭素源として,銅などの基板上にグラフェンを成長させるが,開発した方法はガスの代わりに樟脳(カンファー,C10H16O)やプラスチックなどの固体を用いる。
具体的には,水素(H2)とアルゴン(Ar)の混合ガスをCVD炉に送り込み,個体炭素源から昇華したガスと共に金属基板(銅)に供給することで,基板上にグラフェンの連続膜を堆積する。このとき炭素源は比較的低い温度で昇華するので,核形成速度の制御が可能となり,大きいドメインサイズの単結晶グラフェンが期待できるという。またガスのフローや供給時間をパラメータとすることで層数の制御も可能だとしている。
炭素源として使用する樟脳やプラスチックなど固体炭素原料は,メタンなどの気体炭素源と異なり5員環と6員環から成る炭素分子構造を持つ。研究グループによれば,これらが炭素が6員環の網状につながったグラフェンの成長に効果的な役割を果たし,グラフェン結晶の連続成長を実現できるのだという。
このときのプラスチックは,ポリエチレン,ポリプロピレン,ポリスチレンなどの配合率に依存しないので,廃棄プラスチックが利用できる。また樟脳やプラスチック以外にも間伐材などのバイオマスも利用できるという。廃棄物を用いることができるので環境面で優れるだけでなく,従来のCVD法と比較して原料面でのコストメリットも大きい。設備面でもガスの冷却プロセスが不要なので,関連する設備やそのランニングコストも削減することができる。
研究グループは開発したCVD法を用い,最大10×15cm程度の高品質連続グラフェンシートの作製に成功している。現状では使っている炉(環状炉)の炉管の直径が横幅の限界になっているが,もっと大きな炉を使ったり,ロールツーロールを採用したりすることで,原理的にはさらに大きなシートも作れるとしている。
今回の方法に限らず,CVD法では銅基板からグラフェンシートを他の基板に転写する方法が課題となっている。研究グループではアクリル樹脂を用いる方法により,銅基板に堆積したグラフェンシートを高品質にポリエチレンへ転写することに成功しているが,まだ課題が残っているとして高い転写技術を持つ企業との共同研究を希望している。
また,成膜技術については単結晶粒の更なる大粒子化を目指すとしている。グラフェン膜は成長した結晶同士が結合してできるが,接合界面で結晶構造が崩れることがあり,これが品質に影響を与えることが知られている。大粒子化と共に結晶の方向などが制御できれば,膜の特性がさらに向上することが期待できる。
グラフェンシートの実用化を巡っては様々な研究・発表がされており,最も競争の激しい分野の一つとなっている。産業にも利用できる大面積のシートは特に注目が集まっており,実用化に先鞭をつけることは大きなインパクトを持つ。研究の今後の成果が注目される。